Welding and custom fabrication are two distinct processes in the metalworking industry, each with unique characteristics and applications. Welding refers to joining two pieces of metal by melting their edges and adding a filler metal, resulting in a strong bond. This technique has been utilized for centuries to combine metals durably. On the other hand, custom fabrication is a more encompassing term. It refers to creating metal structures from scratch, starting with raw materials. This involves various cutting, bending, shaping, and assembling techniques. While welding can be a part of the custom fabrication process when joining parts, not all custom fabrication involves welding. Both methods are essential in constructing various metal products, from everyday items to specialized equipment.
Key Processes Involved
Welding: A Multi-Step Procedure
1. Preparing the Metals
- Metals should be thoroughly cleaned and free from oxidation, dirt, oil, and other contaminants to ensure a clean and strong weld.
2. Technique Selection
- Choose the most suitable welding technique based on metal type, desired weld strength, and specific project requirements.
- Common methods include arc welding and gas welding.
3. Application of Heat and Pressure
- Melt the edges of the metals to be joined.
- This might involve electricity (arc welding) or a flame (gas welding), depending on the technique.
4. Cooling and Solidification
- Post-welding, metals undergo a cooling phase.
- Proper cooling determines the final strength and appearance of the weld, avoiding issues like warping or weak spots.
Custom Fabrication: A Detailed Exploration
1. Designing and Planning
- The foundation of any custom fabrication project.
- It involves understanding client needs, sketching designs, and preparing blueprints.
- Ensures the final product aligns with the envisioned result and specifications.
2. Cutting or Shearing
- Initial shaping of the raw metal material.
- Tools like lasers, plasma cutters, and shearing machines might be employed.
- Precision is key to ensuring each piece fits perfectly in the later stages.
3. Forming or Bending
- Giving the metal its desired shape.
- Techniques may include press brakes, rollers, or even manual hammering for specific designs.
- Proper forming ensures the structural integrity of the final product.
4. Assembling or Joining
- Different components are brought together.
- This stage may involve welding, riveting, bolting, or other joining methods.
- The goal is to create a cohesive structure from the individual pieces.
5. Finishing
- The final touches to enhance the product’s appearance and longevity.
- This can include painting to prevent rusting, polishing for a smooth finish, or adding protective coatings.
- Quality finishing not only improves aesthetics but also the product’s durability.
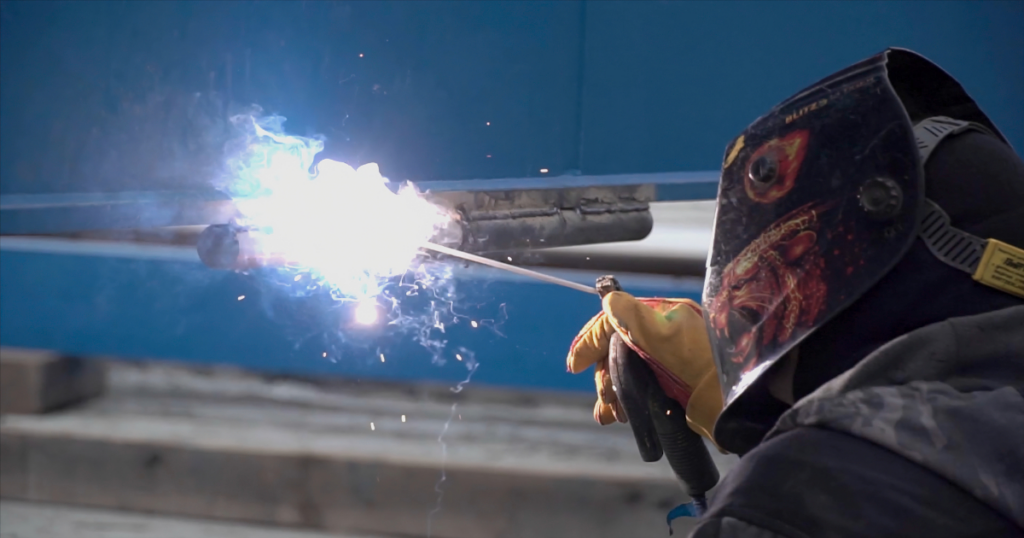
Tools and Equipment
Welding
Welding Machine: The heart of the welding process, welding machines produce the necessary heat and energy to melt metals. This could be through electric arcs or gas flames, depending on the method.
Electrodes or Filler Materials: These play a dual role. They act as a conduit for the electric current in methods like arc welding and, when melted, serve as a filler to create strong bonds between the metals being joined.
Protective Gear (helmets, gloves): Safety is paramount in welding. Helmets shield eyes from intense brightness and harmful ultraviolet and infrared rays, while gloves protect hands from heat, sparks, and molten materials.
Custom Fabrication
Cutting Tools (lasers, plasma cutters): These are indispensable for shaping raw metal into desired parts. Lasers offer precision cuts, especially for intricate designs, while plasma cutters are perfect for thicker metals, providing fast and clean cuts.
Forming equipment (press brakes, rollers): Once cut, metals often need bending or forming. Press brakes provide accurate bends at specific angles, and rollers create curved sections or cylindrical shapes in metal sheets.
Assembly Tools (rivets, bolts, welders): Combining individual pieces requires reliable joining methods. Rivets and bolts offer mechanical fastening, ensuring parts stay connected under stress, whereas welders melt and fuse metal edges, ensuring a solid and long-lasting bond.
Applications and Use Cases
Welding
Repairing Broken Metal Items: Welding is frequently employed to mend broken metal objects, from household items to industrial equipment. The item’s integrity is restored by fusing the broken parts, often extending its lifespan.
Joining Beams in Construction: In construction, welding is essential. It ensures beams and other structural elements are securely joined, providing the necessary strength and stability for buildings and bridges.
Automotive Assembly: The automotive industry heavily relies on welding. It’s used to assemble various car components, from the chassis to the body panels, ensuring vehicles are robust and safe for road use.
Custom Fabrication
Creating Metal Furniture: Custom fabrication shines in the furniture industry, allowing designers to bring unique visions to life. Custom-made pieces can elevate any space’s aesthetic, from sleek metal chairs to ornate wrought-iron tables.
Building Custom Automotive Parts: For car enthusiasts and specialized vehicles, off-the-shelf parts might not suffice. Custom fabrication allows for creation of tailored automotive components that cater to specific performance or design needs.
Crafting Architectural Structures: Beyond basic construction, custom fabrication plays a role in developing unique architectural elements. Whether it’s a bespoke staircase, decorative metal facades, or artistic installations, these custom creations add a signature touch to buildings and landscapes.
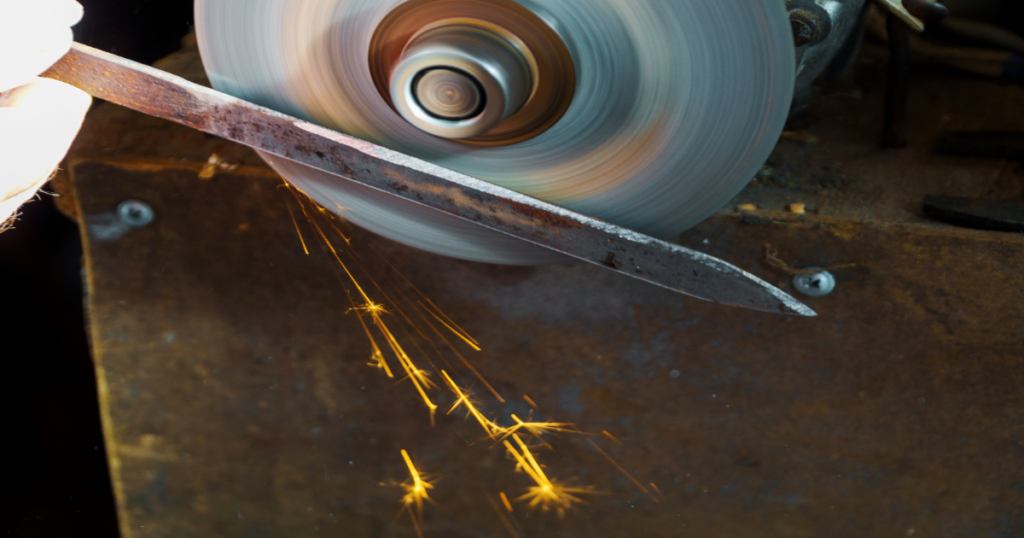
Skills and Expertise Required
Welding
Knowledge of Different Welding Techniques: Different welding methods suit different tasks and materials. A skilled welder must be well-versed in arc welding, gas welding, and TIG/MIG welding to select and apply the best method for the job.
Ability to Work with Precision: Welding requires a steady hand and a keen eye. Ensuring that the metals align correctly and that the weld is consistent across the joint is crucial for the strength and appearance of the finished product.
Understanding of Metals and Their Properties: Different metals have varying melting points, conductivities, and reactions to heat. A good welder must understand these properties to determine the best welding method and ensure a durable bond without damaging the materials.
Custom Fabrication
Design and Blueprint Reading: An essential skill in custom fabrication is the ability to interpret and execute designs from blueprints. This ensures the final product aligns with the envisioned specifications and meets client expectations.
Proficiency in Various Fabrication Tools: Custom fabrication involves a range of tools, from cutting lasers to press brakes. A fabricator must use these tools efficiently and safely to achieve the desired outcome.
Creativity and Problem-solving: While technical skills are foundational, custom fabrication presents unique challenges. A fabricator’s ability to think creatively and devise solutions on the fly can be the difference.
Safety Measures
Welding
Use of Protective Gear: Welding without appropriate protective equipment can be hazardous. Helmets shield the eyes from intense light and harmful rays, while gloves and protective clothing guard against burns from sparks, heat, and molten metal.
Adequate Ventilation in the Working Area: Welding processes can release harmful fumes and gases. Ensuring good ventilation or using fume extraction systems is essential to prevent inhalation of these toxic substances, keeping the work environment safe for the welder and others nearby.
Custom Fabrication
Use of Safety Equipment: During the fabrication process, there’s a risk of injury from flying debris, sharp edges, or hot surfaces. Wearing safety equipment is crucial to safeguard against these hazards.
Ensuring machinery is in Good Working Condition: Regular maintenance and inspections of fabrication machinery are vital. Working with malfunctioning or worn-out equipment can lead to accidents. It’s imperative to keep machines in optimal condition to ensure the safety and quality of the fabricated products.

Outlook and Trends
Advancements in Technology Leading to New Welding Techniques
As technology evolves, so does the realm of welding. New methods, materials, and machinery are being developed, pushing the boundaries of what’s possible. These advancements improve the efficiency and quality of welds and open up opportunities for working with new materials and complex structures. Innovations in areas like laser welding and underwater welding showcase the industry’s dynamic nature, which continues to adapt to the ever-changing technological landscape.
Increasing Demand for Custom Fabricated Products in Various Secto
The versatility and adaptability of custom fabrication have spurred its demand across diverse sectors. There’s a growing appreciation for tailored solutions, from bespoke architectural installations to specialized industrial components. This trend highlights the shifting consumer preference towards personalized, high-quality products over mass-produced items, leading industries to invest more in custom fabrication to cater to these niche demands.
Emergence of Automation in Both Welding and Fabrication
Automation is revolutionizing the welding and fabrication industries. Robotic welding arms, computerized cutting machines, and automated assembly lines are becoming commonplace, enhancing precision and productivity. While there are concerns about job displacement, the integration of automation also presents opportunities for skilled workers to manage, maintain, and program these advanced systems. The synergy between human expertise and machine efficiency paints a promising future for both sectors.
Analogies for Better Understanding
Welding
Imagine you have a hot glue gun. Instead of gluing paper or plastic, you’re “gluing” metals. When the molten metal from the welding process cools down, it solidifies, binding the metals together, much like how hot glue binds objects. Just as you’d want a smooth and even application with a glue gun, you aim for a consistent and strong bond between metal parts in welding.
Custom Fabrication
Picture a tailor working on a suit. They begin with raw fabric, measure, cut, and then meticulously shape and sew each part together. The goal is to create a garment that fits the wearer perfectly. Similarly, professionals start with raw metal in custom fabrication and create a product tailored to specific needs and specifications through cutting and forming. Just as each suit reflects the tailor’s craftsmanship, each fabricated item showcases the skill and precision of the fabricator.
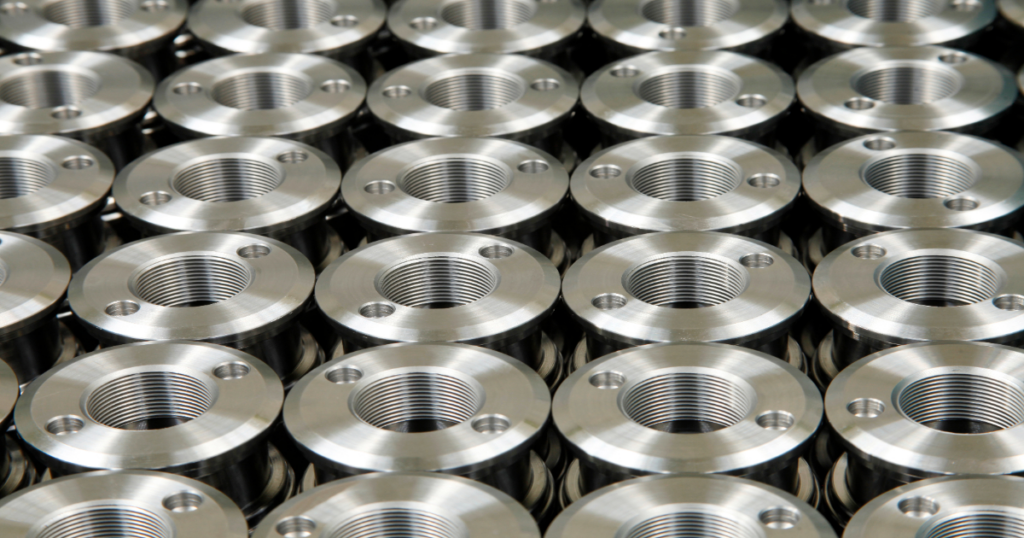
Frequently Asked Questions
What’s the Primary Difference Between Welding and Custom Fabrication?
Welding specifically focuses on combining two pieces of metal by melting their edges. On the other hand, custom fabrication is a broader term encompassing the entire process of creating metal structures, including cutting, shaping, and assembling.
Can Custom Fabrication Include Welding?
Yes, welding can be a part of the custom fabrication process. For instance, welding might be employed when different metal parts need to be joined during the fabrication.
How Has Technology Impacted Custom Fabrication?
Technological advancements have introduced more precise tools, automated machinery, and innovative techniques in custom fabrication, leading to increased efficiency, accuracy, and design possibilities.
Why Is Custom Fabrication Becoming More Popular in Various Sectors?
Custom fabrication offers tailored solutions, allowing industries to get products that precisely fit their unique requirements and specifications. This personalization and high quality are driving its popularity.