Sheet fabrication is a pivotal process in modern manufacturing, serving as the cornerstone of numerous industries. This intricate craft involves the transformation of flat sheets of various materials. From the sleek chassis of automobiles to the precision-engineered aircraft components, sheet fabrication is the unsung hero.
The significance of sheet fabrication lies in its ability to mold raw materials into functional and aesthetically pleasing forms. Its role extends from the automotive and aerospace industries. Moreover, sheet fabrication is a linchpin in the electronics and electrical industries.
Understanding Sheet Materials
Types of Sheet Materials
- Metals
Metals constitute a foundational category of sheet materials in fabrication processes making them indispensable in many applications. Sheet metal, in particular, offers a range of options, including steel, aluminum, and copper, each with distinct characteristics. Steel, prized for its strength and durability, finds extensive use in structural components and machinery.
With its lightweight yet corrosion-resistant nature, aluminum is a favorite in the aerospace and automotive industries. Copper, renowned for its conductivity, is vital in electrical applications. The array of metals available for sheet fabrication provides versatility.
- Plastics
Plastics represent another pivotal category of sheet materials that significantly influence sheet fabrication. These versatile materials, derived from synthetic polymers, encompass various options, each with unique properties and applications. Thermoplastics are known for their flexibility and ease of processing, making them ideal for packaging and consumer goods applications. Thermosetting plastics renders them essential in industries where high-temperature environments are a concern.
Additionally, engineering plastics like nylon and polycarbonate boast a balance of mechanical strength and chemical resistance. The diversity within the realm of plastic sheet materials underscores their role as adaptable solutions.
- Composites
Composites bring a fascinating dimension to the world of sheet fabrication by combining the best attributes of different materials. These materials consist of a matrix, often a polymer resin, reinforced with fibers or particles. Composites offer a remarkable blend of strength, durability, and lightweight properties.
Carbon fiber composites are celebrated for their exceptional strength-to-weight ratio. Similarly, fiberglass composites exhibit excellent corrosion resistance, rendering them suitable for marine and architectural uses. The adaptability and tailored properties of composite sheet materials make them a compelling choice for engineers and manufacturers seeking innovative solutions in sheet fabrication, underscoring their vital role in shaping advanced products across diverse industries.
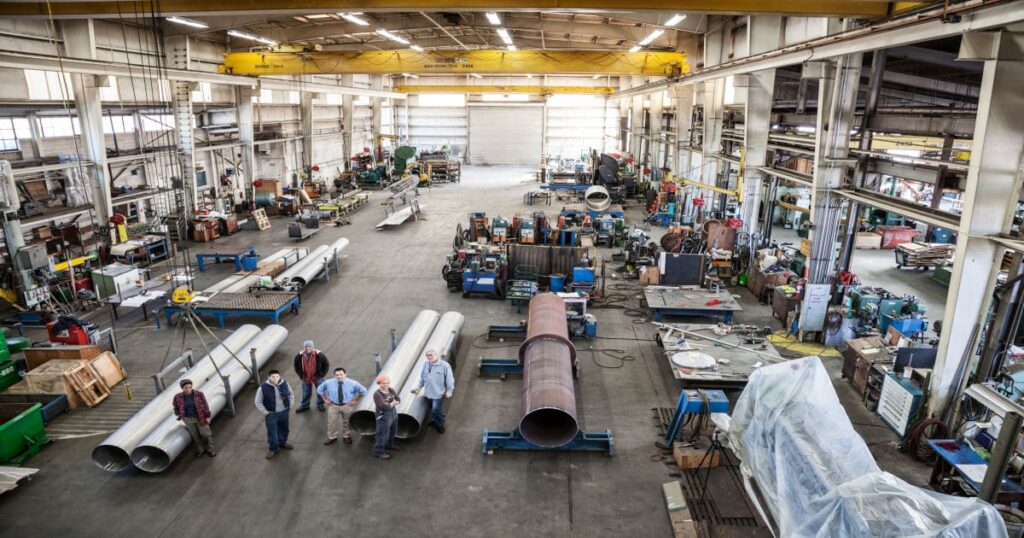
Properties of Sheet Materials
Strength and Durability
Strength and durability are fundamental properties in sheet materials, exerting a profound influence on their suitability for various applications. The strength of a sheet material refers to its ability to withstand external forces without undergoing deformation or failure. In sheet fabrication, the choice of material with adequate strength ensures the integrity and reliability of the final product.
On the other hand, durability pertains to a material’s ability to withstand long-term exposure to environmental factors such as moisture, temperature variations, and corrosive substances without degrading or losing functionality. This property is especially critical in applications where the sheet material is expected to have a prolonged lifespan, such as architectural cladding or outdoor equipment. Materials like stainless steel and certain engineered plastics are renowned for their durability, making them popular choices when resilience to harsh conditions is paramount.
Conductivity
Conductivity is a property in sheet materials, profoundly impacting their applicability in various industries. Electrical conductivity, which measures a material’s ability to transmit electrical current, is pivotal in electronics and electrical engineering. Compounds like copper and aluminum, renowned for their high electrical conductivity, are indispensable in manufacturing electrical wiring, printed circuit boards, and power transmission components.
Also, thermal conductivity, which gauges a material’s capacity to conduct heat, is paramount in industries where heat management is critical. With their exceptional thermal conductivity properties, materials like copper and aluminum are favored in applications such as heat sinks and radiators. By rapidly dissipating heat, these materials help maintain the optimal operating temperatures of electronic components and machinery, preventing overheating and ensuring the reliability and longevity of various devices.
Corrosion Resistance
Corrosion resistance is a critical property in sheet materials, particularly in industries where exposure to corrosive environments is a constant concern. This property signifies a material’s capability to withstand the detrimental effects of moisture, chemicals, or other corrosive agents over time.
Stainless steel, renowned for its exceptional corrosion resistance, is a prime example of a material prized for resisting deterioration even in harsh conditions. This makes it a preferred choice in applications such as architectural cladding, where exposure to coastal saltwater is common, and in chemical industries where aggressive substances are handled. Furthermore, materials like fiberglass-reinforced plastics (FRP) are widely adopted for their corrosion resistance in environments with a high risk of material degradation.
Sheet Fabrication Methods
Cutting and Shearing
The cutting and shearing processes in sheet fabrication are foundational, initially transforming flat sheet materials into intricate components and structures. A key aspect of this stage is the selection of cutting techniques, with laser and plasma cutting as prominent methods. Laser cutting, renowned for its precision, involves meticulously using a focused laser beam to cut through sheet materials. This method is favored in applications requiring intricate and detailed cuts.
Plasma cutting, in contrast, employs a high-velocity jet of ionized gas to swiftly and efficiently cut through sheet materials, making it particularly suitable for thick metal sheets. This technique’s versatility in handling various materials has earned it a place of prominence in industries like automotive manufacturing, shipbuilding, and industrial construction, where rapid and precise cutting is essential.
Bending and Forming
Bending and forming are essential techniques in sheet fabrication, allowing flat sheet materials to be shaped into three-dimensional components and structures. Various methods are employed to achieve these transformations, each offering distinct advantages depending on the desired outcome and the material used.
Press Brake Bending: Press brake machines are commonly used for the precision bending of sheet materials. A punch-and-die setup exerts a force on the sheet, causing it to bend along a predetermined line. This method is suitable for producing precise angles and consistent bends. It finds extensive use in industries like metalworking, where tight tolerances are critical.
Rolling: Rolling involves passing the sheet material through a set of rollers that gradually bend it into a curved shape. This method is particularly effective for creating cylindrical or conical shapes, making it valuable in manufacturing pipes, tanks, and architectural elements.
Hydraulic Press Forming: Hydraulic presses utilize hydraulic cylinders to exert force on the sheet material, gradually forming it into the desired shape. This method is versatile and can be used for simple and complex shapes. It is often employed in the aerospace and automotive industries to produce intricate components.
Stretch Forming: In stretch forming, the sheet material is stretched and clamped over a die, resulting in a deformation of the material into the desired shape. It is commonly used for applications requiring smooth, curved surfaces, such as aircraft fuselages and architectural features.
Incremental Sheet Forming: This innovative technique uses a CNC-controlled tool to shape the sheet material gradually through small, incremental movements. It is well-suited for prototyping and creating complex, freeform shapes with minimal material waste.
Joining and Welding
Joining and welding are integral processes in sheet fabrication, allowing multiple pieces of sheet material to be securely connected, forming cohesive structures or components. There are several welding methods, each offering distinct advantages and applications in the sheet fabrication process.
MIG Welding (Metal Inert Gas)
MIG welding is a widely used method that involves feeding a consumable wire electrode through a welding gun, which melts and fuses with the base metal. An inert gas shields the welding area from contamination, typically argon or a mixture of gases.
TIG Welding (Tungsten Inert Gas)
TIG welding uses a non-consumable tungsten electrode, which generates heat to melt the base metal and a separate rod if needed. A shielding gas, usually argon, protects the weld from oxidation. TIG welding offers exceptional control over the welding process, producing high-quality, precise welds.
Spot Welding
Spot welding joins two or more metal sheets by applying pressure and passing a high electrical current through the sheets at localized points. This method is especially prevalent in the automotive industry for assembling body panels and components.
Arc Welding
Arc welding encompasses various techniques, such as Stick (SMAW), Flux-Cored (FCAW), and Submerged Arc (SAW) welding, where an electric arc is established between an electrode and the base metal. The heat generated melts the materials, and additional filler metal may be added if necessary.
Resistance Welding
Resistance welding techniques include spot welding, as mentioned earlier, as well as seam welding and projection welding. These methods use the resistance generated by electrical currents to heat and fuse the materials at specific points or along seams.
Finishing and Surface Treatment
Surface treatment is a pivotal aspect of sheet fabrication, playing a role in enhancing the functionality, aesthetics, and longevity of fabricated components and structures. It involves various processes and techniques to modify the surface properties of sheet materials, and its importance cannot be overstated.
Corrosion Protection: One of the primary reasons for surface treatment is corrosion protection. Many sheet materials, such as steel and aluminum, are susceptible to corrosion. Surface treatments like painting, powder coating, and galvanizing create a protective barrier that shields the material from moisture, chemicals, and oxidation. This significantly extends the lifespan of components and structures, reducing maintenance costs and ensuring long-term durability.
Aesthetic Enhancement: Surface treatment is instrumental in enhancing the visual appeal of fabricated products. Painting, for instance, allows for various colors and finishes, making it ideal for consumer goods, automotive components, and architectural elements. Powder coating provides an attractive finish that is resistant to chipping and fading, further elevating the aesthetics of products.
Functional Improvement: Surface treatments can also improve the functional properties of sheet materials. Anodizing, for example, enhances the corrosion resistance of aluminum while providing a decorative finish. Lubrication and anti-friction coatings reduce friction and wear in moving parts, making them suitable for machinery and automotive components.
Adhesion and Bonding: Surface treatment can improve adhesion and bonding properties, facilitating the attachment of adhesives, sealants, or coatings to the sheet material. This is crucial in industries like aerospace and automotive, where strong and reliable bonds are essential for structural integrity.
Hygiene and Cleanability: In applications where hygiene is paramount, such as food processing or healthcare, surface treatments like electro-polishing can create smooth, easy-to-clean surfaces that prevent the accumulation of contaminants.
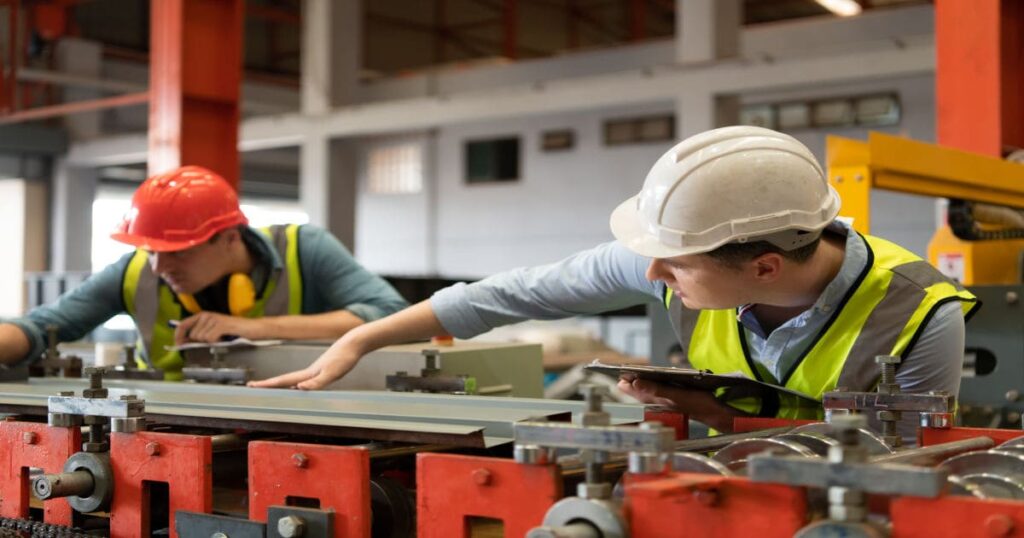
The Fabrication Process
Design and Planning
Design and planning represent the foundational stages of the sheet fabrication process, and their significance cannot be overstated. They are paramount as they lay the groundwork for the fabrication process. Careful planning ensures that the fabricated components or structures meet their intended purpose efficiently and effectively.
Material Selection
Material selection is a pivotal aspect of the sheet fabrication process, with numerous factors influencing the choice of the most suitable material for a particular application. These factors encompass various considerations, including mechanical properties like strength, durability, and flexibility, essential for ensuring the final product’s structural integrity. Moreover, factors such as corrosion resistance and thermal conductivity play a role in determining material compatibility with the intended environment and application.
Cost considerations are also paramount, impacting the project’s budget and feasibility. Material availability, ease of fabrication, and sustainability also guide the selection process, ensuring that the chosen material aligns with the project’s goals, performance requirements, and long-term environmental impact.
Cutting and Shaping
Material Preparation: The sheet material is selected based on the project’s requirements, considering material type, thickness, and desired properties.
Design and Layout: The specific shapes and dimensions needed for the component or structure are determined by the project’s design specifications.
Cutting: The sheet material is cut along the predetermined lines using various cutting techniques, such as laser cutting, plasma cutting, or mechanical shearing.
Bending and Forming: In this phase, the cut sheet is shaped into the desired three-dimensional form using techniques like press brake bending, rolling, or hydraulic press forming.
Joining: If the final product requires multiple components to be assembled, joining processes such as welding, riveting, or adhesive bonding connect the parts securely. These methods ensure structural integrity and cohesion.
Quality Control: Throughout the cutting, shaping, and joining processes, rigorous quality control measures are implemented to check for dimensional accuracy, material defects, and proper alignment. Any deviations from the design specifications are addressed and corrected.
Surface Treatment: After fabrication, the component may undergo surface treatment processes like painting, powder coating, or anodizing to enhance its appearance, protect against corrosion, or improve functional properties.
Final Inspection: The finished component undergoes a final inspection to ensure it meets all quality and performance standards. This includes verifying dimensions, tolerances, and overall functionality.
Assembly (if applicable): If the component is part of a larger assembly, the assembly team integrates it into the final product, making any additional connections or fastenings as needed.
Packaging and Delivery: The manufacturers appropriately package the fabricated components for protection during transportation and deliver them to their intended destination, ready for installation or use.
Joining and Welding
One of the most widely used methods is MIG welding. At the same time, an electric arc melts the materials, resulting in a robust fusion weld. TIG welding, on the other hand, relies on a non-consumable tungsten electrode and shielding gas, offering precise control and producing clean, high-quality welds.
Spot welding, a resistance welding process, uses high electrical current to create weld spots, making it efficient for automotive applications. Arc welding encompasses various techniques where an electric arc forms between an electrode and the base material, suitable for various materials and industries. Lastly, resistance welding includes spot, seam, and projection welding.
Quality Control
Quality control is a critical aspect of sheet fabrication, ensuring that products meet rigorous standards of precision and performance. Inspection and testing methods ensure that fabricated components adhere to design specifications and industry regulations. Visual inspection is often the first step, involving meticulously examining the component’s surface for defects, irregularities, or imperfections.
Dimensional inspection uses precise measurement tools to verify that the component’s dimensions align with the intended design. Non-destructive testing methods detect hidden flaws or structural defects without damaging the component. Additionally, destructive testing methods like tensile and impact testing can assess the material’s mechanical properties.
Final Assembly
Final assembly is the end of the sheet fabrication process, where all the meticulously crafted components come together. This phase involves integrating individual parts, including sheet metal components, welded structures, or other fabricated elements. Skilled technicians meticulously follow assembly instructions and drawings, ensuring they correctly position and securely fasten each component.
Workers conduct quality checks during the final assembly phase to confirm that all parts are correctly aligned. This stage ensures the fabricated components function harmoniously, fulfilling their intended purpose in various industries.
Applications of Sheet Fabrication
Automotive Industry
Sheet fabrication plays a vital role in the automotive sector. Its lightweight yet durable properties make it essential for enhancing fuel efficiency and ensuring vehicle safety.
Aerospace Industry
In aerospace, sheet fabrication contributes to constructing aircraft structural components, lightweight yet strong materials.
Construction and Architecture
Sheet fabrication is instrumental in constructing architectural elements like facades, roofing, and structural components for buildings. Its versatility in terms of material and design enables the creation of innovative and aesthetically pleasing structures.
Electronics and Electrical
The electronics and electrical industries use sheet fabrication to craft casings, enclosures, and heat sinks. Its ability to provide functional and aesthetic solutions is paramount in this sector.
Consumer Goods
Sheet fabrication finds application in consumer goods, contributing to manufacturing items such as appliances, furniture, and decorative items. Its versatility and adaptability enable the creation of various consumer products with varying shapes and functionalities.
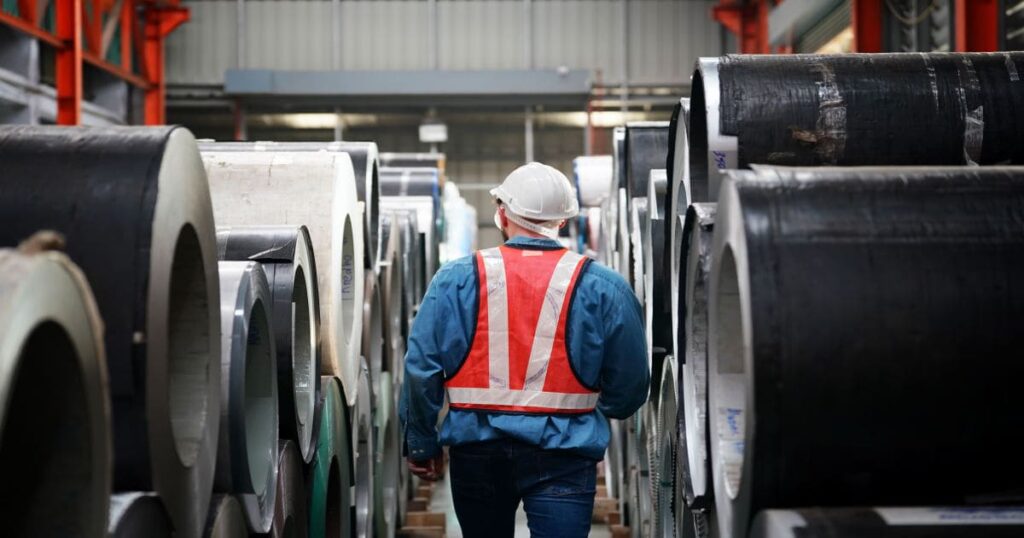
Advancements in Sheet Fabrication
Technological Innovations
Automation and Robotics
Technological advancements in sheet fabrication have led to increased automation and the integration of robotics into the manufacturing process. Automated systems equipped with robotics can perform tasks such as cutting, bending, and welding with remarkable precision and efficiency. This not only reduces labor costs but also enhances the consistency and speed of production. Moreover, using advanced sensors and computer-aided design (CAD) systems allows for real-time monitoring and adjustments, ensuring optimal quality and minimal material wastage.
3D Printing in Sheet Fabrication
3D printing has begun to revolutionize sheet fabrication, creating complex and customized components with unprecedented ease. In this process, sheets of material are built up layer by layer, offering design flexibility and reducing material waste. 3D printing is particularly valuable for prototyping and low-volume production, where traditional methods may be cost-prohibitive. Its integration into sheet fabrication opens up new possibilities for innovative designs and efficient manufacturing.
Sustainability in Sheet Fabrication
Sustainability has become a central focus in sheet fabrication, leading to the development and adoption of eco-friendly materials and processes. Manufacturers increasingly use recyclable and renewable materials in their sheet fabrication operations, reducing the environmental footprint of their products. Additionally, advances in water-based coatings and low-VOC (volatile organic compound) paints contribute to environmentally responsible finishing processes.
Furthermore, manufacturers are incorporating energy-efficient equipment and practices, such as laser cutting and efficient heating methods, to minimize energy consumption in sheet fabrication. These sustainability initiatives align with global efforts to reduce the environmental impact of manufacturing, making sheet fabrication a more responsible and eco-conscious industry.
Challenges and Future Trends
Challenges in Sheet Fabrication
Cost Constraints: One of the persistent challenges in sheet fabrication is managing cost constraints while maintaining high-quality standards. The fluctuating prices of raw materials, energy costs, and competitive pricing pressures can make it challenging for manufacturers to optimize their profit margins without compromising material quality and product performance.
Skilled Labor Shortage: As sheet fabrication becomes increasingly technologically advanced, there is a demand for skilled labor capable of operating and maintaining sophisticated machinery and understanding complex CAD systems. The shortage of skilled workers poses a challenge, as it can impact production efficiency and product quality.
Future Trends
We expect that digitalization and the principles of Industry 4.0 will heavily influence the future of sheet fabrication. Manufacturers embrace smart manufacturing technologies, IoT (Internet of Things) integration, and data analytics to optimize production processes, monitor equipment performance, and reduce downtime. This trend will lead to more efficient and responsive sheet fabrication operations, where machines communicate and adapt in real-time, improving productivity, quality, and overall competitiveness in the industry. Additionally, technological advancements will further enhance predictive maintenance and process optimization in sheet fabrication, offering new possibilities for cost reduction and increased efficiency.
The Ever-Expanding Horizons of Sheet Fabrication
As this comprehensive overview explores, sheet fabrication is dynamic and indispensable in modern manufacturing. It weaves together the intricate cutting, shaping, joining, and welding processes fueled by material science and technological advancements. Meticulous design considerations, quality control, and sustainability initiatives hold immense significance. Moreover, the industry is on the cusp of transformation through digitalization and the principles of Industry 4.0. It promises more efficient and responsive operations. The future of sheet fabrication is bright, with innovations like 3D printing and smart manufacturing poised to redefine the landscape.
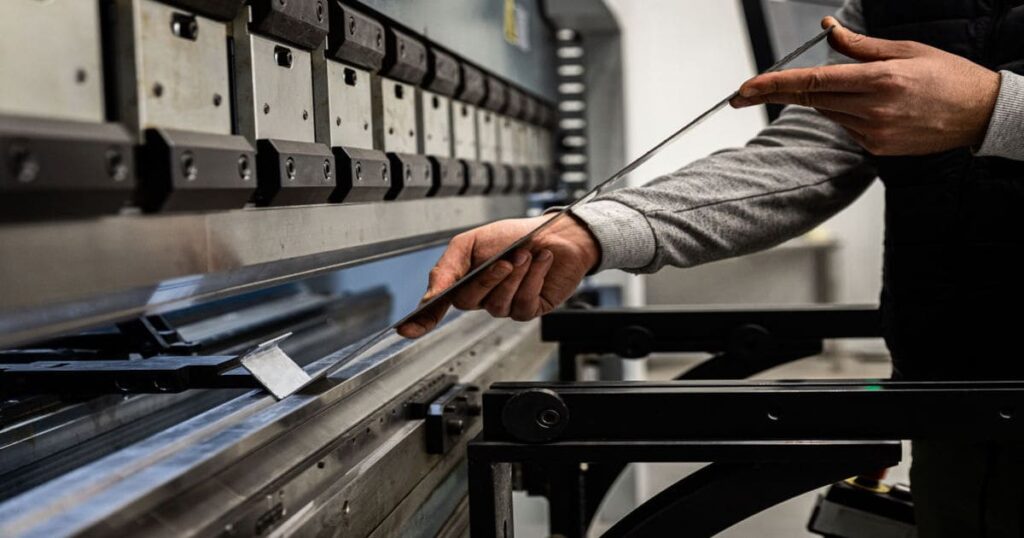
Frequently Asked Questions
How Does the Cutting and Shaping Process Work in Sheet Fabrication?
The cutting and shaping involve techniques like laser cutting, plasma cutting, bending, and forming. Manufacturers use these methods to cut sheet materials into desired shapes and bend them to achieve specific geometries, ensuring precision and accuracy in the final product.
Why is Quality Control Important in Sheet Fabrication?
Quality control ensures that fabricated components meet design specifications and industry standards. It involves inspection, testing, and validation to ensure the final product’s structural integrity, functionality, and safety.
How is Sustainability Integrated into Sheet Fabrication Processes?
Companies address sustainability by using eco-friendly materials, implementing energy-efficient processes, and launching waste reduction initiatives. Manufacturers are increasingly adopting practices that minimize the environmental impact of sheet fabrication.
How Can I Stay With the Latest Developments in Sheet Fabrication?
You can stay informed about sheet fabrication developments by accessing industry publications, attending trade shows, and utilizing online resources dedicated to manufacturing and engineering. Additionally, connecting with professionals in the field and joining industry organizations can provide valuable insights into the latest trends and innovations.