The metal fabrication industry is a cornerstone of modern manufacturing, playing a pivotal role in producing components and structures for sectors like automotive, aerospace, and construction. This industry encompasses diverse processes, including welding, cutting, bending, and assembling, where raw metal materials are transformed into predefined shapes and products. Its importance lies in its ability to tailor solutions to specific industrial needs, driving innovation and efficiency across numerous fields.
Role of Metal Fabricators Across Industries
Metal fabricators are instrumental in many industries, providing essential components that underpin the functionality and integrity of various products and structures. From creating vital parts for machinery in the manufacturing sector to contributing to the intricacies of architectural designs in construction, their expertise ensures durability, precision, and innovation. This reliance underscores the fabricators’ significance in maintaining these key sectors’ continuous advancement and efficiency.
Complexities of Sourcing Skilled Metal Fabricators
Securing skilled metal fabricators has become a critical challenge, marked by a competitive landscape and evolving industry demands. This difficulty stems from a growing skills gap, where the need for advanced technical expertise and adaptability in handling modern fabrication technologies outpaces the supply of trained professionals. This scenario impacts production timelines and affects the overall quality and innovation in projects relying on metal fabrication.
Exploring the Essence of Metal Fabrication
Metal fabrication is a sophisticated process that involves the manipulation of metal to create structures, machines, and other components through various techniques such as cutting, bending, welding, and assembling. This process transforms raw metal materials into precise, finished products tailored to specific design requirements. It is the backbone for numerous industries, translating designs and blueprints into tangible, functional items.
Core Processes in Metal Fabrication
At the heart of metal fabrication lie several key processes: cutting, which involves slicing through metal to create specific shapes; bending, which shapes the metal into desired angles and forms; and assembling, where individual pieces are joined to form complex structures. Each of these processes requires a unique set of skills and machinery, playing a crucial role in transforming raw metal into finished products that meet exacting standards of strength, precision, and durability.
Diverse Industries Dependent on Metal Fabrication
Metal fabrication is an indispensable part of various industries, each relying on its precision and versatility. The construction industry heavily depends on it for structural components like beams and frames. Creating parts ranging from simple brackets to complex engine components is crucial in the automotive sector. Aerospace relies on metal fabrication for airframe structures and critical flight components. Additionally, consumer goods, from appliances to electronics, often incorporate metal-fabricated parts, showcasing the industry’s broad impact and versatility.
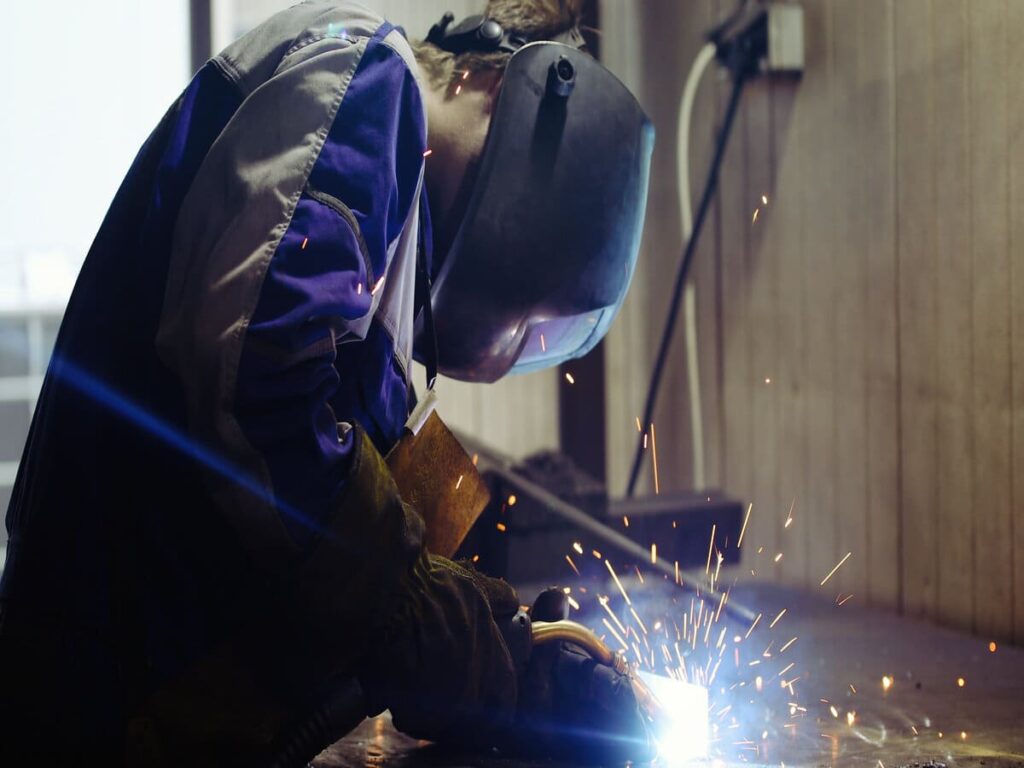
Essential Skills for Effective Metal Fabrication
Effective metal fabrication demands a comprehensive skill set, combining technical proficiency with precision and creativity. Key among these skills is expertise in welding, cutting, and machining, enabling fabricators to manipulate metal accurately. Knowledge of different metals and their properties is crucial for selecting the right material for each project. Additionally, skills in reading and interpreting blueprints and technical drawings are essential for translating design concepts into physical components. Proficiency in using various tools and machinery, along with a strong understanding of safety protocols, further contributes to the efficiency and quality of the fabrication process.
Precision and Quality Control in Metal Fabrication
In metal fabrication, precision and quality control can ensure the integrity of the final product. Precision in cutting, shaping, and assembling metal parts is essential to meet stringent tolerances required in many applications, particularly in the aerospace and automotive industries, where even minor deviations can have significant consequences. On the other hand, quality control ensures that each piece meets established standards and specifications, guaranteeing reliability and safety. This dual focus on precision and quality not only enhances the performance and longevity of fabricated components but also upholds the reputation and trustworthiness of the fabricators in a highly competitive market.
Cultivating Expertise in Metal Fabrication through Experience and Training
The combined impact of experience and training is indispensable in shaping a skilled workforce in metal fabrication. Experience offers a practical, hands-on understanding of the craft, honing a fabricator’s ability to manage complex projects and unforeseen challenges. Concurrently, structured training provides a foundational knowledge of techniques, safety protocols, and emerging technologies, ensuring that fabricators are well-equipped to meet the industry’s evolving demands with proficiency and innovation.
Challenges in Finding Skilled Metal Fabricators
Scarcity of Trained Professionals: The metal fabrication industry faces a significant challenge in the scarcity of trained professionals, exacerbated by an aging workforce and a lack of new talent. This shortage impacts the industry’s capacity to maintain quality and meet production deadlines.
Gap Between Industry Needs and Educational Training: A notable gap exists between the specific skill sets required in the metal fabrication industry and the training provided by educational institutions. This mismatch often leaves new entrants underprepared for the complex and evolving demands of the industry.
High Demand and Competitive Market for Skilled Fabricators: The demand for skilled metal fabricators is intensifying, fueled by growth in sectors like construction and manufacturing. This led to a competitive market where attracting top talent is challenging for companies.
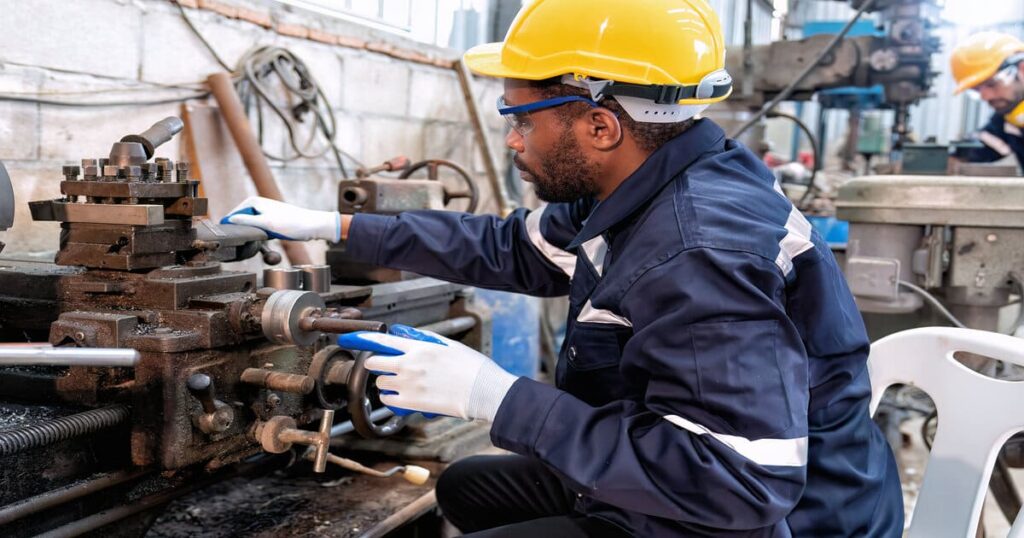
Revolutionizing Metal Fabrication with Emerging Technologies
Emerging technologies are dramatically transforming the landscape of metal fabrication, introducing unprecedented levels of precision, efficiency, and versatility. Advancements such as 3D printing, laser cutting, and automation are streamlining production processes and enabling the creation of more complex and intricate designs. These innovations push the boundaries of what’s possible in metal fabrication, necessitating a workforce equally adept in traditional skills and new technological methodologies.
Adapting to Rapid Technological Changes in Metal Fabrication
Maintaining rapid technological advancements in dynamic metal fabrication is a formidable challenge. As the industry evolves with innovations like robotics, AI, and advanced CNC machinery, fabricators and companies continuously need to update skills and adapt processes. This requirement for ongoing education and investment in new technologies is essential to stay competitive and maintain high standards of quality and efficiency.
Embracing Continuous Learning and Flexibility in Metal Fabrication
In the ever-evolving world of metal fabrication, ongoing training, and adaptability is crucial for maintaining industry relevance and competitiveness. Continuous upskilling allows fabricators to stay abreast of new techniques and technologies, ensuring their skill sets remain aligned with industry advancements. This commitment to lifelong learning and flexibility is vital for both individual career growth and the overall progression of the metal fabrication industry.
Upholding Standards and Regulations for Quality Assurance in Metal Fabrication
Adhering to industry standards and regulations is best in the metal fabrication industry to ensure the highest levels of quality and safety. These guidelines, encompassing everything from material specifications to fabrication processes, are critical in delivering products that meet safety, durability, and performance criteria. Compliance with these standards safeguards the end-users and enhances the credibility and reliability of the fabricating entities in a highly competitive market.
Ensuring Consistent Quality: A Persistent Challenge in Metal Fabrication
Maintaining consistent quality across all projects presents a notable challenge in the metal fabrication industry. This difficulty stems from variables like fluctuating material properties, varying skill levels of workers, and the complexity of different fabrication processes. Achieving uniformity in quality demands rigorous quality control measures and a well-trained, attentive workforce, ensuring that every fabricated component meets the stringent standards expected by clients and industries.
Consequences of Substandard Metal Fabrication in Projects and Industries
The impact of poor quality fabrication in the metal industry is profound, often leading to critical project failures and tarnishing entire industries’ reputations. Inadequate fabrication can result in structural weaknesses, leading to safety risks, costly repairs, or complete project overhauls. For industries where precision is non-negotiable, these quality lapses can lead to significant financial losses and erode consumer trust, highlighting the necessity of stringent quality control in metal fabrication.

Geographical Variations in Skilled Metal Fabricator Availability
Regional disparities significantly impact the availability of skilled metal fabricators, creating challenges in certain areas while offering abundance in others. In many industrialized regions, there’s a concentration of highly trained fabricators, whereas remote or less developed areas often face a scarcity of such skilled professionals. This uneven distribution affects not only local project execution but also influences the broader dynamics of the metal fabrication industry, including cost, quality, and the feasibility of undertaking complex projects in certain locations.
Resource Availability: Influencing Quality and Costs in Metal Fabrication
The availability of resources, plays a crucial role in determining the quality and cost-effectiveness of metal fabrication. Regions rich in resources and talent tend to produce higher-quality outputs at competitive prices. Conversely, areas with limited access to quality materials or skilled professionals often face increased costs and challenges/
Economic Trends Shaping Skilled Labor Availability in Metal Fabrication
Economic fluctuations play a role in shaping the availability of skilled labor in the metal fabrication industry. In periods of economic growth, there’s an escalated demand for fabricated products, leading to a higher demand for skilled workers. However, the industry often struggles to meet demand due to a limited pool of trained professionals. Conversely, the demand for fabrication decreases during economic downturns. The surplus skilled labor available often faces challenges in securing stable employment, reflecting the cyclical nature of labor availability.
Market Fluctuations and Their Impact on the Metal Fabrication Industry
Market fluctuations significantly influence the metal fabrication industry, affecting everything from raw material costs to client demand. In times of economic prosperity, the industry often sees an uptick in demand. However, the industry can face challenges during economic downturns or market instability.
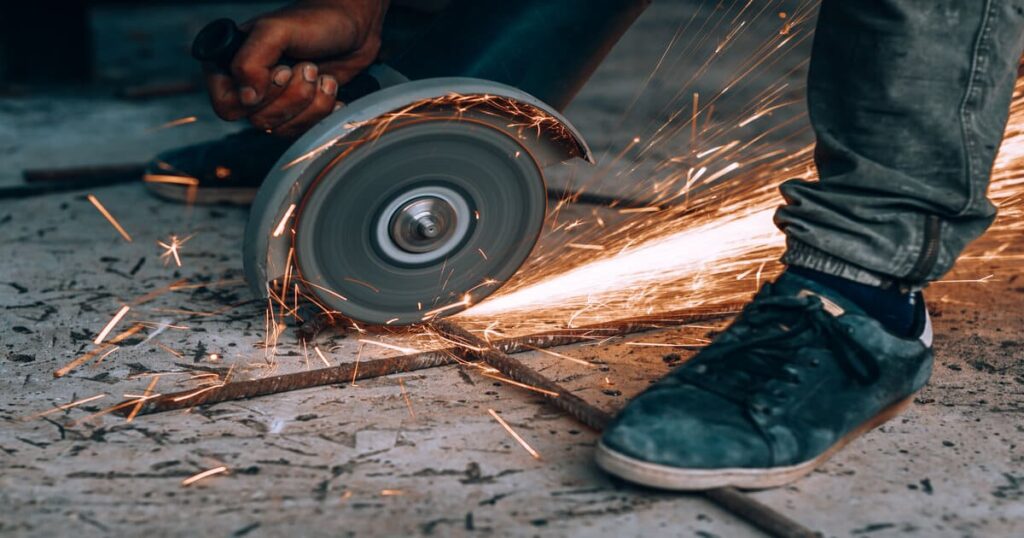
Strategies to Overcome Skill Shortages in Metal Fabrication
A multi-faceted approach is essential to bridge the skill gap in the metal fabrication industry. This includes enhancing vocational training to align with industry needs, fostering apprenticeships for practical experience, and forging partnerships. Additionally, promoting continuous learning within organizations and broadening talent recruitment efforts can help create a skilled workforce.
Role of Apprenticeship and Training in Metal Fabrication
Apprenticeship and training programs are vital in cultivating the next generation of skilled metal fabricators. These programs provide a blend of theoretical education and hands-on experience. It is essential for mastering the intricate techniques and technologies of the trade. These programs are instrumental in ensuring a competent and proficient workforce that can meet the industry’s evolving demands.
Approaches for Recruiting and Retaining Metal Fabrication Talent
To attract and retain skilled metal fabricators, businesses must implement strategic approaches. Additionally, investing in continuous training and career development opportunities can create an environment that encourages long-term employment and professional growth. Creating a positive workplace culture focusing on safety, respect, and employee engagement.
Addressing Challenges and Envisioning the Future in Metal Fabrication
In conclusion, the challenges in sourcing skilled metal fabricators stem from a scarcity of trained professionals, a gap between educational training, and intense market competition. The metal fabrication industry must adapt to these challenges by embracing new technologies, enhancing training programs, and diversifying recruitment strategies. With these adaptations, the industry can anticipate a future where a skilled and adaptable workforce drives innovation and excellence. It ensures this vital’s continued growth and relevance.
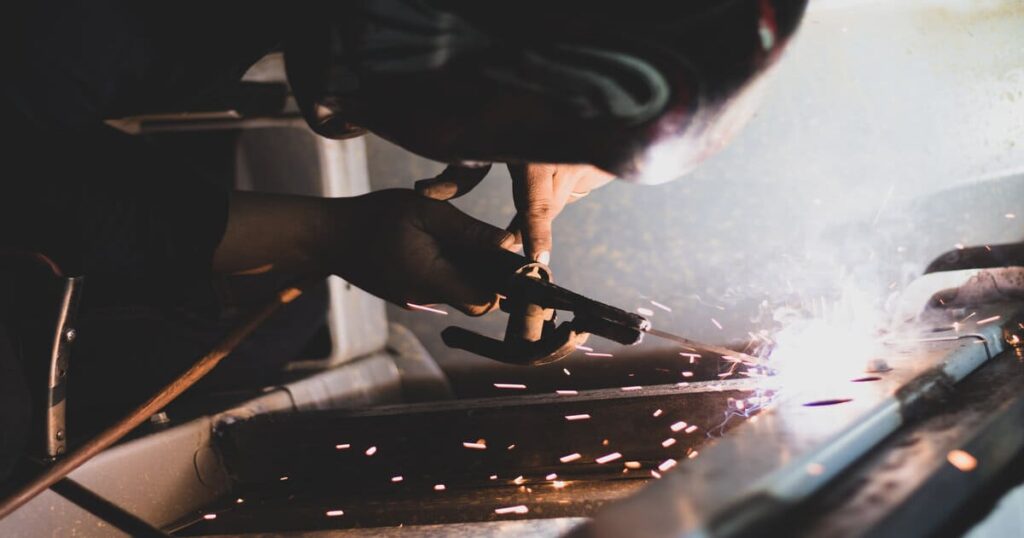
Frequently Asked Questions
Why is There a Gap Between Educational Training and Industry Needs in Metal Fabrication?
This gap often arises from the rapid evolution of technology and techniques in metal fabrication. It leaves new graduates less prepared for the industry’s specific demands.
How Important is Ongoing Training in the Metal Fabrication Industry?
Ongoing training is crucial to keep up with technological advancements and evolving industry standards. It ensures that fabricators’ skills remain relevant and competitive.
What Impact Do Economic Trends Have on the Metal Fabrication Industry?
Economic trends affect the demand for metal-fabricated products, influencing the availability of jobs and the need for skilled labor. Economic growth typically increases demand for fabricators, while downturns can lead to a surplus of labor.
What is the Significance of Apprenticeship Programs in this Industry?
Apprenticeship programs are vital for providing hands-on experience and practical skills. It bridges the gap between theoretical knowledge and the real-world demands of the industry.
Can Technological Advancements Help in Bridging the Skill Gap?
Yes, training advancements such as virtual and augmented reality can simulate real-world scenarios. This provides an efficient way for fabricators to learn and adapt to new techniques and technologies.
What Does the Future Look Like for the Metal Fabrication Industry?
The future of metal fabrication will likely be characterized by continued technological advancement. A greater emphasis on training and skill development and a focus on adapting to changing market demands and workforce dynamics.